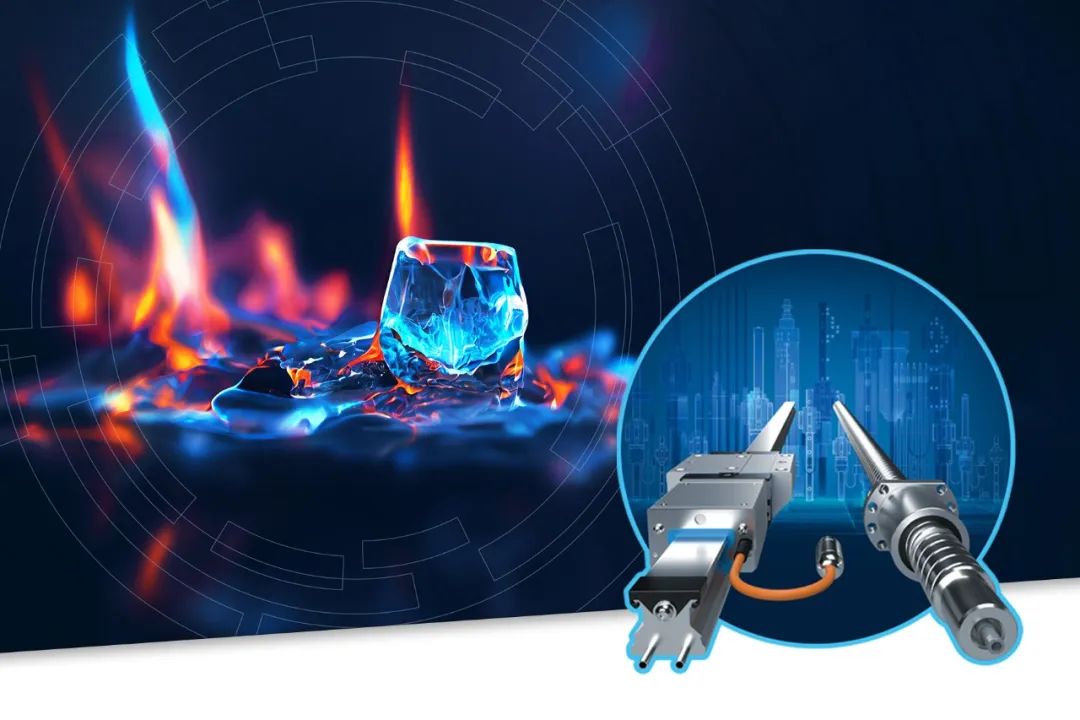
为汽车企业“赋能”的新型轻量化技术,具体是什么样的?
能为企业赋能的新型轻量化技术
轻量化新技术层出不穷德国宝马(BMW)集团将机动车的重量减轻了130kg,德国奥迪(Audi)不甘落后,也将机动车重量减轻了300kg——这些案例表明,汽车车身设计领域正悄然发生一场巨大变革。而引领这场世界改革浪潮的,正是德国汽车制造商。宝马和奥迪两家德国制造商,采用了“多材料实用化”,即复合使用多种材料,打造车身结构的技术。其中,宝马采用了碳纤维增强复合材料(CFRP)、高抗拉强度钢板、铝合金等轻量化材料与普通钢材组合使用的方式,来进行车体结构的设计,并成功将高级四门轿车“7”系列的车身重量减轻了130kg。
同时使用高抗拉强度钢板、多相钢板、铝合金、CFRP和钢板等5种合金,在提高刚性和强度的同时,实现轻量化。另一方面,奥迪公司大胆采用了轻量材料——铝合金。通过组合使用铝合金与高抗拉强度钢板等多种复合材料,设计了新型车身结构,成功将多功能SUV“奥迪Q7”系列的车体重量减轻了300kg。
采用多材料的车身结构。积极地采用铝合金材料,实现汽车减重300kg。宝马和奥迪之所以推进多材料化,是因为以普通钢材为基础的车身设计很难再推动轻量化的进一步发展。也就是说,现有轻量化技术已经碰触到了“边界”。宝马公司表示,“车身形状的设计已基本完成。要想达成更高水准的轻量化,只能将轻量化材料放到合适的地方,让其发挥应有的作用”。未来,推进零件和产品轻量化的开发技术将持续精进。其中起牵引作用,或者说是促进作用的行业,是汽车制造业。当然,这指的并不仅仅是高级乘用车制造商。住友化学认为,“几乎所有的汽车制造商和汽车零件制造商都杀红了眼,拼命想在轻量化中寻求突破”。可见,大家剑锋所指,都是要突破目前的“边界”。
油耗规制的时限,迫在眉睫制造商重视轻量化生产的原因,主要有两个。一,如果不减轻车身重量,让制造出来的产品油耗更低,就无法继续占有市场。因为只有在低油耗竞争中将对手比下去,才能够赢得顾客的青睐。二,油耗规制(二氧化碳排放规制)日益严苛,必须实现超出以往水准的轻量化。以欧洲为中心,油耗规制正以燎原之势遍布世界。不遵守这些规制的制造商,或将被处以高额罚款,并背上“无视环保的无良企业”的恶名,对企业形象造成负面影响。
我们都知道,轻量化是一个横跨制造行业的大课题。那么,为什么率先启动这场轻量化变革的,会是汽车制造商?原因,其实非常简单——油耗规制“时限”迫在眉睫。汽车制造商担忧的,是与世界油耗规制紧密相关的“2020年问题”,即2020年达到日本规定的二氧化碳排放量105kg/km,2021年达到欧洲规定的二氧化碳排放量95kg/km。为了解决这个棘手问题,汽车制造商设置了一个整体的轻量化目标,并以这个目标为准,逐步加工各个零件——先设定整体需要减重多少千克的目标,然后落实到每个零件需要减重多少——进而让目标和进程更加明确。而为了达成这个定额,负责人会想尽一切办法。包含产品评估在内的开发设计流程至少需要花费数年时间,所以,留给制造商的时间确实不多了。
油耗竞争愈演愈烈的情况不仅出现在汽车制造行业。船舶和航空领域也同样厮杀惨烈。在全球竞争日益激烈的今天,很多客户会倾向于选择油耗更低的产品。在产业机器人和机床等领域,制造商通过减轻可移动零件的重量,以实现节能减耗、更高精度的位置移动和更快速的动作。此外,市场还对便携式设备给予了高度关注。通过减轻设备重量,提高便携性,可以在减轻人体身体负荷的同时增强舒适感。轻量化会使市场竞争白热化,因为只要解决轻量化课题,就可以直接提高产品的附加价值。各个领域的轻量化进程都在悄然发生巨变。但是,目前市场需求的,还是可以带领大家突破现有“边界”的新技术、新思维。
顺应节能和降低成本的客户需求:日本做过一份问卷调查,也可以看出客户对于轻量化需求的高涨。该问卷的回答者均为技术人员,我们从中可以看出现实工厂中的实际情况。问卷中有这样一个问题:“当前职务中,您需要完成轻量化目标的原因是什么?”回答“因为客户需要”的,占比42.3%。也就是说,正是因为客户提出了一系列的要求,供应商才不得不达到轻量化的目标。
实现轻量化的重点,是工艺、结构优化和材料选择
为应对前所未有的市场需求,轻量化新技术层出不穷,大有突破现有边界的势头。从符合实用水准的轻量化技术的角度来看,轻量化大致可以从“工艺、结构优化”和“材料选择”两个方向入手。
工艺、结构优化的典型案例,是多材料化,即着眼于产品整体,把轻量化材料进行“适材、适所”的组合,以削减整体重量,确保必要处的强度。例如,“宝马7系列”的车身钢板变得更轻薄,是因为宝马公司为了补充材料的强度,使用了强度更高的CFRP作为补充材料。这种设计,可以保证更高的材料强度和刚性,实现按普通思路很难达到的轻量化程度。这项技术,可以将不同材料直接进行焊接或粘合,改变产品结构,以实现轻量化。也就是说,不必再使用连接用的螺栓和螺母等类似产品,以及为了连接而生产的其他零件(比如法兰接头)了。
如此一来,结构会变得更加简单。为确保焊接、粘合强度,需要重新整理产品评价标准和体制。突破这一课题,达到实用化水准的先例,是赢创工业(daicel-evoni,总部位于日本东京都)。赢创工业采用将铝合金和聚酰胺(PA)两种不同材料进行牢固焊接的工艺,成功研发了前端模块。与在传统的钢架结构中安装树脂材料相比,产品减轻了20%左右。JR东海公司通过采用大幅减少散热量的碳化硅(SiC)电力半导体,实现了新干线驱动系统的轻量化,并通过将系统构成较为复杂的强风冷装置转换为结构较为简单的行驶风冷装置,使车体成功减重20%。
采用轻质材料:通过“材料选择”改进轻量化技术,是指将现有材料替换为较为轻便的材料,或充分发挥原有材料的作用,以实现轻量化。新型轻量材料的代表,就是CFRP(碳纤维增强复合材料)。CFRP具有量产规模优势,因此汽车行业对CFRP给予了高度关注。汽车行业以外的其他行业也在积极推进CFRP的应用。比如,NAKASHIMA PROPELLER(总部位于日本冈山市)将船舶用螺旋桨的材料从铜合金替换为CFRP,成功将螺旋桨减重50%。提高树脂材料耐热性的动向也更为明显,制造商纷纷尝试在更高温的环境中应用树脂。
具体来看,汽车的引擎、变速器等周边零件都由传统的金属材质转变为高耐热树脂。住友电木株式会社将两轮机动车引擎中铝合金材质汽缸组的一部分,替换为碳素纤维和玻璃纤维强化的酚醛树脂,最大减重可达28%。住友化学开发了高耐热性的聚醚砜树脂(PES),通过将汽车引擎油量控制阀从铝合金材质替换为PES,成功使阀重减轻50%,并投入量产。丰田纺织开发出了由聚丙烯(PP)和聚酰胺11(PA11)构成的耐冲击材质——聚合物合金,并研发出了发泡成型工艺,生产出世界最轻量级的门饰板。这种门饰板通过了侧面冲击等强力冲击试验,被评定为不易损坏材质。与致力于“车身多材料化”的宝马和奥迪形成鼎足之势的,是日本丰田公司。
丰田表示“要将钢材质进行到底”。丰田管理人员认为,轻量化的关键,在于“充分利用高抗张钢板”。在这一大背景下,日本铁钢制造商将发挥巨大作用。新日铁住金可以生产抗张力高达1000Mpa的超高抗张钢板,其优势不仅是生产高抗张力钢板,还能为汽车制造商等提供包括加工技术和生产技术在内的解决方案——高抗张力钢板的强度虽然高,但却十分轻薄;钢板或将出现半面、成型加工性能较差等问题。新日铁住金通过提供配套的理论支持和加工技术,让客户深深感受到了钢材的优势。
(转载)