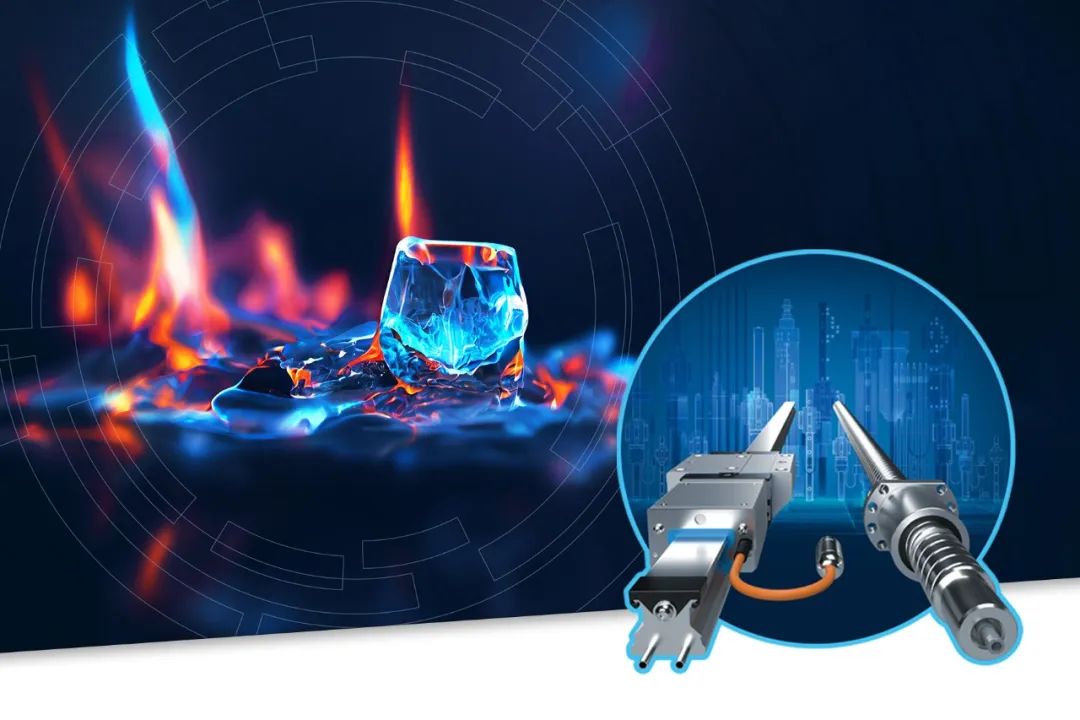
汽车的制造中,发动机是最关键最核心的部件,俗称汽车的“心脏”。它是一辆汽车中最为复杂和最能体现制造技术的部分,而气缸体是发动机的主体,它将各个气缸和曲轴箱连成一体,是安装活塞、曲轴以及其他零部件的支承骨架,同时气缸体内部集成了发动机中大部分油道。油道主要作用是供高压润滑的机油通过,柴油机油道压力通常在290kPa以上,油道一旦泄漏,将导致严重的后果。在制造中,油道的密封性能必须得到保证。
问题提出
我司引进美国福特汽车的PUMA发动机,并建造了自己的缸体、缸盖、曲轴及连杆的机加工生产线和整机装配线。生产线设计产能10.3万台/年,其中缸体生产线孔类加工全部使用德国双交换托盘卧加工中心。发动机投产三年后,售后先后反馈有500km新车发动机漏油。仔细查看漏油部位,主要是从发动机缸体后端面主油道孔口渗出,孔口密封方式为抽芯铆钉。进一步拆除抽芯铆钉查看失效原因 ,发现主油道孔内有明显的螺旋状刀纹(图1 ),刀纹用指甲触碰有所感知。同时,拆除一台不渗油的缸体,孔内部无异常刀纹。查找投产前三年记录,无发动机油道漏油反馈,查找投产时封存的样件,无刀纹问题。
图1 主油道孔内螺旋状刀纹
初步原因分析
针对主油道孔内螺旋状刀纹产生的原因,我们首先对加工工艺进行梳理:根据主油道孔的产品图纸(图2),得知主油道孔总深度427mm,孔径φ16(-0.16,+0.32)mm,孔内粗糙度Ra6.3mm。根据主油道引导孔直槽钻图纸(图3),得知刀具直径是φ16.18 mm(H7)。根据深孔麻花钴图纸(图4),得知刀具直径是¢16.15mm(H7)。
图2 主油道孔的产品图纸
图3 主油道引导孔直槽钻图纸
图4 深孔麻花钻图纸
加工顺序:首先引导孔直槽钻在后端面和前端面分别钻孔,深度分别是110mm和118 mm;第二步是麻花钻在前端面钻孔深度190mm,然后在后端面钻孔深度250mm,钻通主油道孔。加工完成后以F5000的速度进行退刀。
初步原因:通过对直槽钻加工后暂停加工,我们发现直槽钻加工完后孔内光滑无刀纹,再继续使用麻花钻加工,刀纹出现,螺旋刀纹的间距和退刀速度匹配。初步确定刀纹的产生是由麻花钻退刀导致,同一台机床螺旋刀纹时有时无。
根本原因分析
经过判断,我们确定螺旋刀纹是深孔麻花钻退刀时造成的,对于造成深孔麻花钻退刀纹产生的原因,我们从以下方面进行分析:
工件:测量有刀纹和无刀纹工件定位面和定位孔,尺寸合格、外形相同,无其他干涉造成影响;测量工件硬度分别为208HB和210HB,符合图纸要求的187~241HB要求;工件成分组织测量无异常。通过以上判断,初步可排除工件原因导致退刀纹。
夹具:检查双托盘夹具压块锁紧螺母,拧紧正常;检查机床自动夹紧状态下的压头和压块,无松动;夹具定位销直径和定位面测量正常;夹紧状态下表显托盘夹紧压力为240bar(1bar=105Pa), 在要求的210~260bar范围内。通过以上判断,初步可排除夹具原因导 致退刀纹。
刀具:实测引导直槽钻直径为φ16.17mm,符合φ16.18mm(H7) 要求;实测深孔麻花钻直径为φ16.13mm,符合φ16.15mm(H7) 要求;实测深孔麻花钻径向圆跳动0.007mm,符合要求;引导钻和 深孔麻花钻之间设计预留的间隙为0.04mm,符合间隙要求;
机床:使用激光干涉检测仪对机床重复定位精度进行检测,实测为0.0029mm,符合0.005mm 以内要求;架表实测机床主轴径向近端圆跳动为0.008mm,远端为0.021mm;侧母线为0.014mm,符合要求。观察机床换刀过程,确认深孔麻花钻刀柄与主轴结合无夹杂铁屑等脏物,机床主轴换刀吹气功能 正常;在液压站出口处连接压力表,监测液压站输出压力稳定。
程序:深孔麻花钻快进转攻进时安全距离预留为3mm,实测为3mm正常;深孔麻花钻快退速度为F5000;尝试更换以F2000快退速度并试加工,刀纹变得更加密集,波纹之间间距变小。
根据以上验证,加上新引导孔麻花钻和深孔钻头累计修磨使用寿命是15~20次。综合判断: 刀具修磨质量、直径、跳动和机床主轴跳动等综合原因最终导致螺旋刀纹的偶发性出现。
解决方法
1.方案一
目前使用的引导钻和深孔钻都是修磨刀具,把引导钻和深孔钻更换成新刀(未修磨)并加工 验证,共加工10件,出现1件刀纹工件,增加引导孔和深孔钻 之间钻孔间隙,为验证间隙对刀纹的影响,人为把麻花钻的直径修磨至φ16.05mm,引导钻直径保持不变,引导钻和深孔麻花钻之间间隙提高至0.12mm。把修磨后的深孔麻花钻用机床进行加工验证。共加工10件工件,出现2件螺旋刀纹工件。
2. 方案二
把后端面引导孔深度从110mm分别降低至70mm和50mm,同时把深孔麻花钻的攻进位置缩短70mm和50mm,与引导孔深度相匹配。在其他条件未改变情况下进行加工验证, 两种距离各加工10件工件,分别出现4件和3件螺旋刀纹,此方案无法消除刀纹。
3. 方案三
在按现有工艺方案引导钻和深孔麻花钻加工完成的基础上,在后端面主油道孔孔口增加一把铰刀进行铰削,铰削深度与抽芯 铆钉相匹配。
根据产品设计方确认,抽芯铆钉不能进行直径更改,故要预留铰削余量必须对孔口的直径 进行缩小。在保留孔口直径匹配 抽芯铆钉不变的情况下,需对引导孔和深孔麻花钻的刀具进行变更。经过和刀具工程师、产品设计工程师确认,引导直槽钻直径从φ16.18mm(H7)改为φ15.73mm(H7),深孔麻花钻直径从φ16.15mm(H7)改为φ5.7mm(H7),铰刀直径设计为φ16.2mm,铰削长度为15mm。改进后的直槽钻、麻花钻、铰刀装用机床进行铰削加工实验。实验共加工58件,未发现异常螺旋刀纹工件。经过数据统计分析,改进后孔径的能力数据,改进前后的主油道孔孔内照片如图5所示。通过在麻花钻后增加铰刀的加工方式,问题得到解决。
图5 改进前后的主油道孔孔内照片
总结
综上所述,本文通过工件、夹具、刀具、机床及程序等因素进行单个分析确认,最终发现各因子之间按照对应的标准并无明显的异常。在所有因子中,刀具因素产生的影响最为突出,主机厂钻头类如麻花钻和深孔钻头等累计循环修磨使用15~20次才达到报废标准。综合判断:刀具修磨质量,刀具直径、跳动和机床主轴跳动等综合原因最终导致螺旋刀纹的偶发性出现。我们在不影响质量和不增加其他隐患的前提下,通过增加铰刀加工消除此问题。